We often see upper and lower bearings engraved on connecting rod bearings, but many people don’t know why there is such a distinction.
The connecting rod bearings of internal combustion engines are divided into upper bearings (the upper part of the big end of the connecting rod) and lower bearings (the lower part of the big end of the connecting rod).
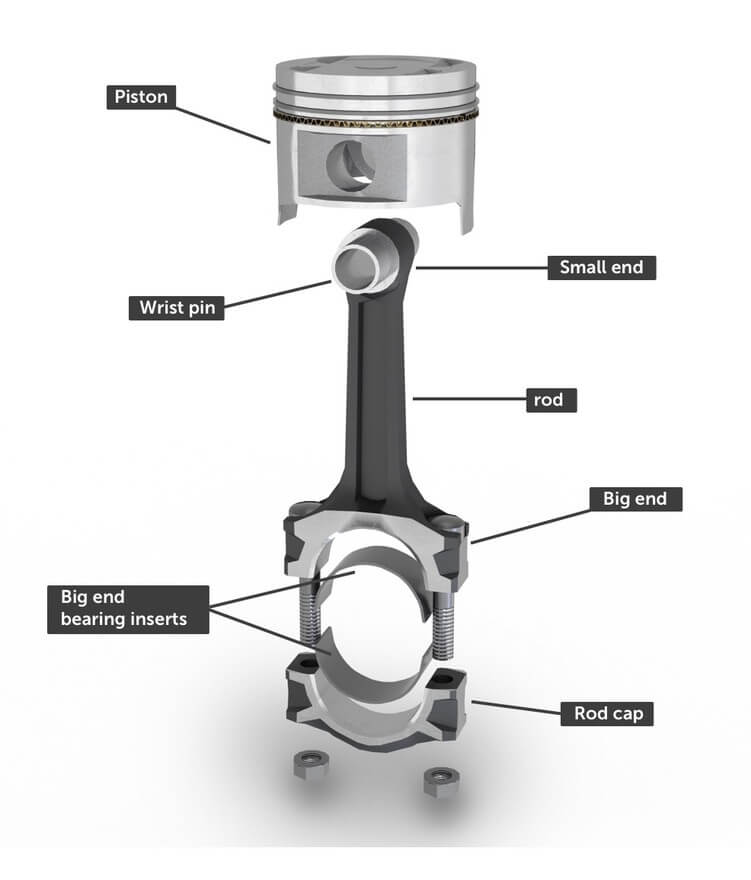
This split design is a very important technical detail in the design of internal combustion engines. The core reasons can be attributed to the following points:
________________________________________
**1. Structural adaptability and installation convenience
• Crankshaft and connecting rod matching:
The connecting rod needs to be connected to the connecting rod journal (crank pin) of the crankshaft through the big end. Since the crankshaft is an integral structure (cannot be split), the split upper and lower bearing design allows the big end of the connecting rod to “wrap” the crankshaft journal, thereby completing the assembly. If an integrated connecting rod bearing is used, it cannot be installed on the crankshaft.
• Disassembly and maintenance:
The split design allows only the connecting rod cap (lower bearing part) to be removed during maintenance without completely disassembling the engine, greatly simplifying the maintenance process.
________________________________________
**2. Optimization of load distribution
• Uniform load bearing:
When the internal combustion engine is working, the big end of the connecting rod is subjected to periodically changing explosion pressure (combustion stroke) and inertia force. The split design allows the load to be evenly transmitted to the crankshaft journal through the upper and lower bearings, avoiding local wear caused by concentrated force on one side.
• Fitting accuracy:
The upper and lower bearings form a high-precision fit with the crankshaft journal through precision machining, and the split structure makes it easier to control the gap (such as the standard gap is 0.02~0.05mm), ensuring lubrication and reducing friction.
________________________________________
**3. Adaptation of the lubrication system
• Oil film formation:
The split design allows the lubricating oil to enter from the oil hole at the big end of the connecting rod, and evenly distribute through the parting surface between the upper and lower bearings to form a stable oil film, reducing friction and wear.
• Oil channel design:
Many connecting rod bearings have oil grooves or oil holes designed at the joint surface of the upper and lower bearings. The split structure facilitates the circulation of lubricating oil and pressure maintenance.
________________________________________
**4. Compensation for thermal expansion
• Material thermal deformation:
When the internal combustion engine is running, the crankshaft and connecting rod will expand due to high temperature. The split design allows the upper and lower bearings to have a certain degree of free deformation when heated to avoid jamming or deformation caused by thermal stress.
• Clearance adjustment:
The split structure can compensate for the clearance change caused by temperature change by adjusting the preload of the connecting rod bolts to ensure long-term stable operation.
________________________________________
**5. Economical manufacturing and maintenance
• Processing feasibility:
The manufacturing process of the split connecting rod bearing is simpler. The upper and lower bearings can be manufactured separately by precision casting or machining, and then combined by bolt tightening, which reduces the difficulty and cost of processing.
• Replaceability:
If the bearing bearing is worn, only one side (upper or lower bearing) needs to be replaced or replaced in pairs, without replacing the connecting rod as a whole, which significantly reduces the maintenance cost.
________________________________________
**6. Control of dynamics and vibration
• Inertial force balance:
The split design of the upper and lower bearings helps to balance the inertial force generated by the reciprocating motion of the connecting rod and reduce the vibration of the crankshaft system.
• Fatigue life improvement:
The split structure disperses the impact of the alternating load on the bearing, delays the occurrence of fatigue cracks, and prolongs the service life.
________________________________________
The design of the split connecting rod bearing (upper bearing + lower bearing) is one of the core technologies for efficient and reliable operation of internal combustion engines. It solves the key problems in the matching of crankshaft and connecting rod by optimizing load distribution, lubrication, thermal management, and simplifying manufacturing and maintenance. If an integrated design is adopted, it will not only be impossible to assemble it on the crankshaft, but also lead to uneven lubrication, increased local wear, and even cause serious engine failures (such as “burned bearings” or “seized shafts”).